3M VHB Acrylic adhesive Double-sided FoamTape Strong Adhese Pad IP68 Waterproof High-quality Reuse Home Car Office Decor 5608
Adhesives & Sealers>>>Home Improvement
Brand Name OIMG
Origin CN(Origin)
DIY Supplies Woodworking
Certification CE
Certification FCC
Certification PSE
Model Number VHB AA8809
is_customized Yes
Type Tape
Color
10mm
15mm
20mm
30mm
40mm
50mm
5mm
Length
3M
33M
Thickness
0.8mm
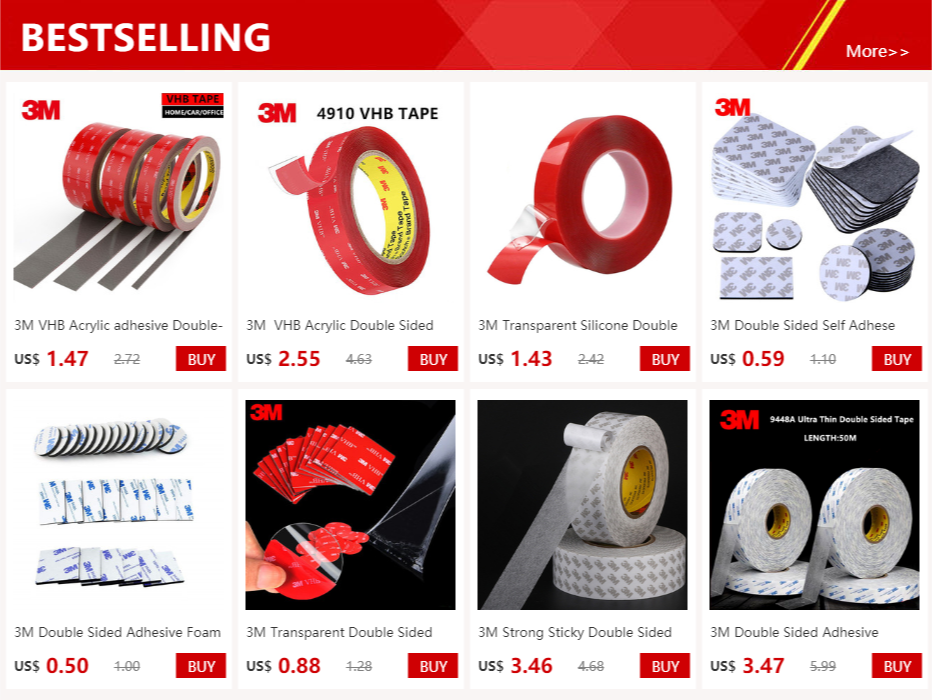








Application Guidelines :
✔ 50% strength of bond in 20 minutes, 90% strength of bond in 24 hours, and 100% strength of bond after 72 hours.Note: Clean the work surface, make sure it's smooth and clean. Please stick and let sit for 24 hours, the longer the more viscous.
Specification
двухсторонний скотч
Quality :original 3M prodcut.Color : GreyThickness :0.8mmLength: 3m /33m(as your choose)Width:5mm/10mm/15mm/20mm/30mm/40mm/50mmAdhesive on both sides3M Strong Permanent Double Sided Super Self-Adhesive Sticky Tape Roll Adhesive
Fast and easy-to-use permanent bonding method provides high strength and long-term durabilityVirtually invisible fastening keeps surfaces smoothCan replace mechanical fasteners (rivets, welding, screws) or liquid adhesivesGrey, thickness: 0.8mm, modified acrylic adhesive and very conformable acrylic foam core bonds to a wide variety of substrates including powder coated paints and irregular surfacesRelative Adhesion:HSE – High Surface EnergyLSE – Low Surface EnergyAnti-temperature :93°C~149°CApplication:Typical applications include: body side moldings; stainless steel, ABS and PVC rocker panels; wheel lip moldings, door edgeFeatures:3M acrylic foam tape is characterized by high performance peel and shear adhesion, high internal strength, good conformability and excellent plasticizer resistance.
Package Included:
1 x 3m Double Sided tape

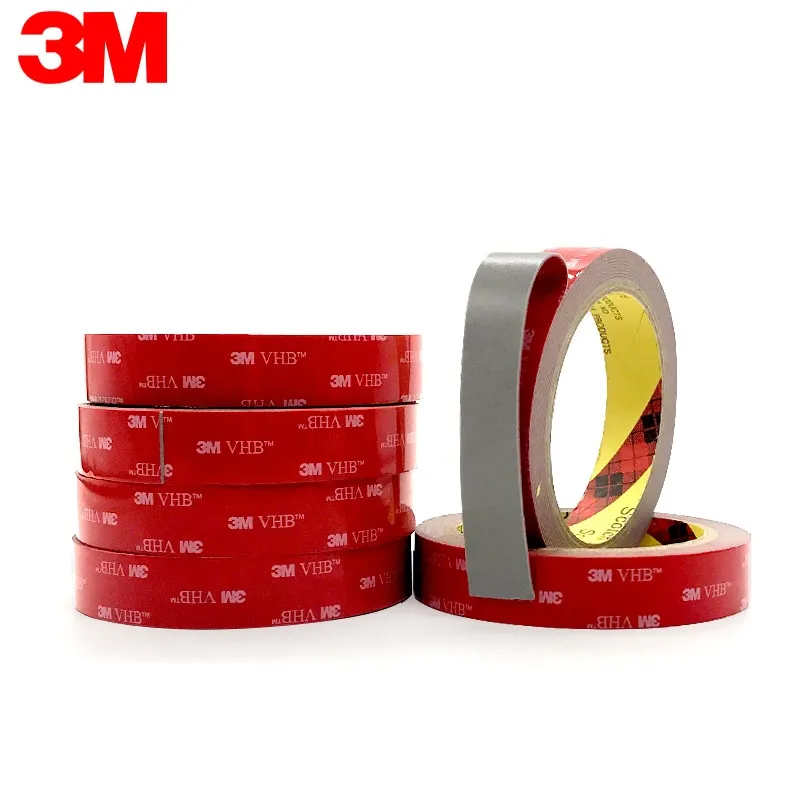
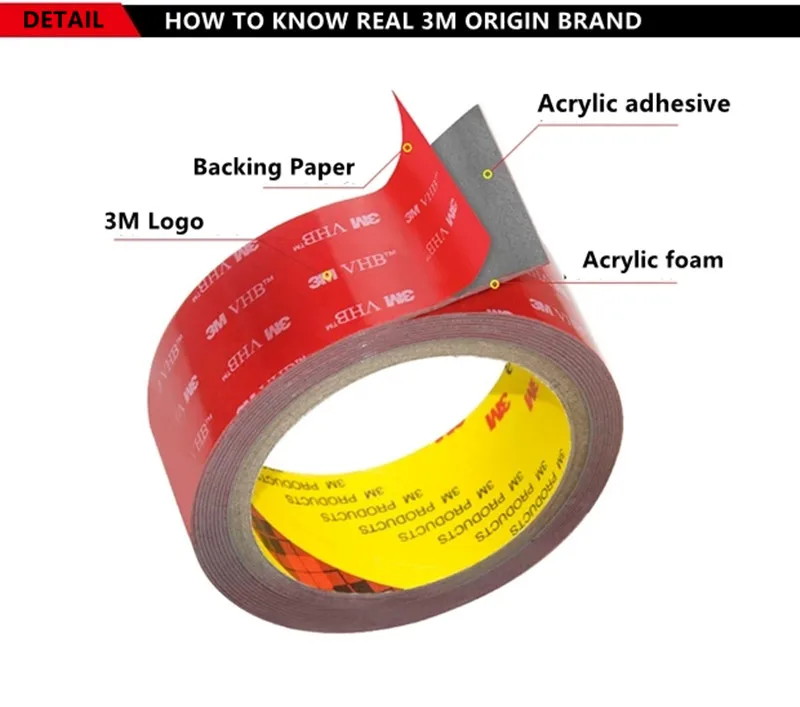

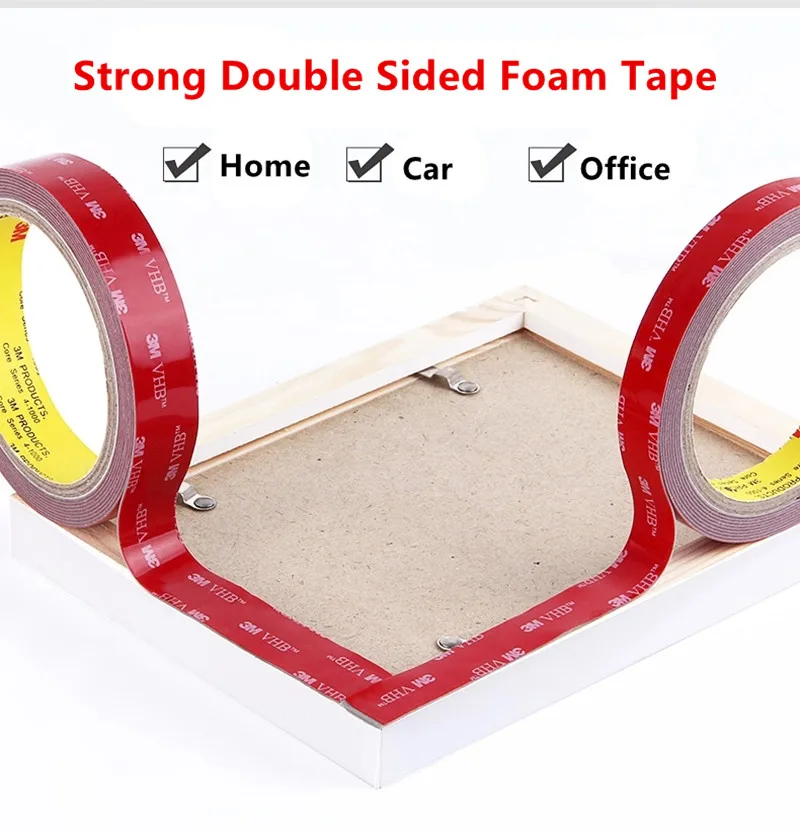

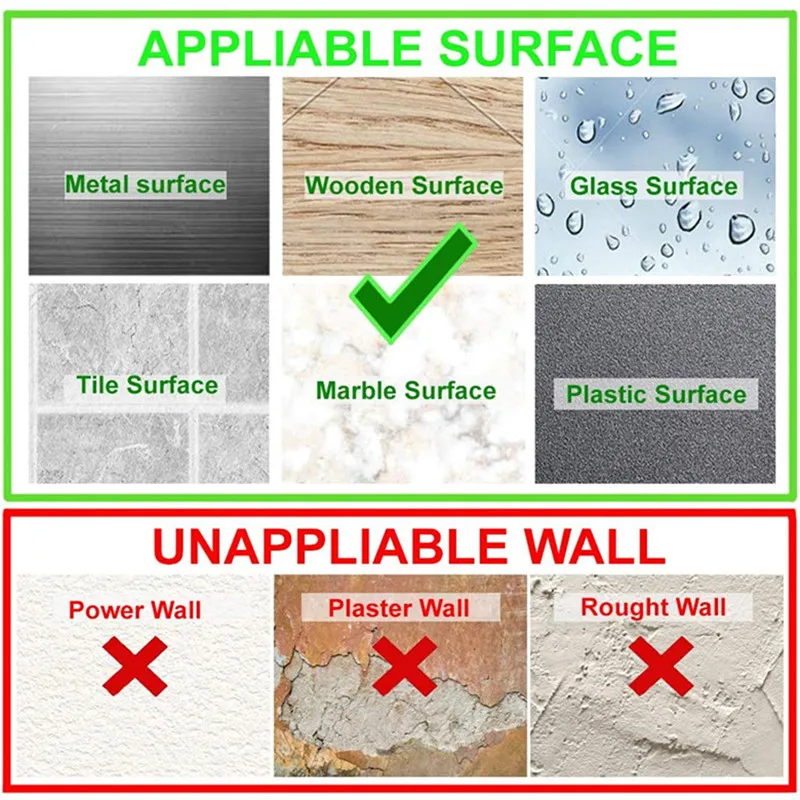
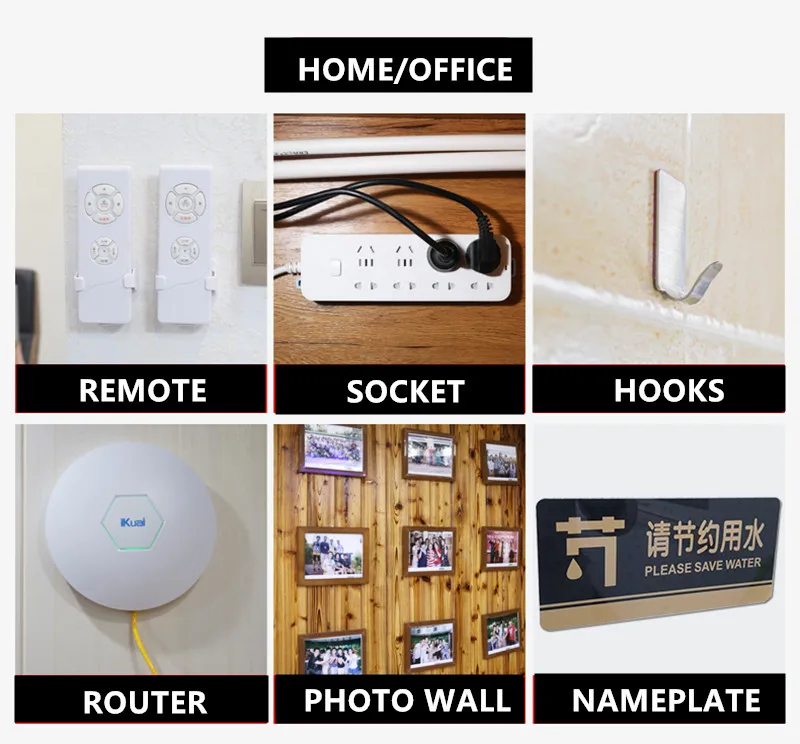

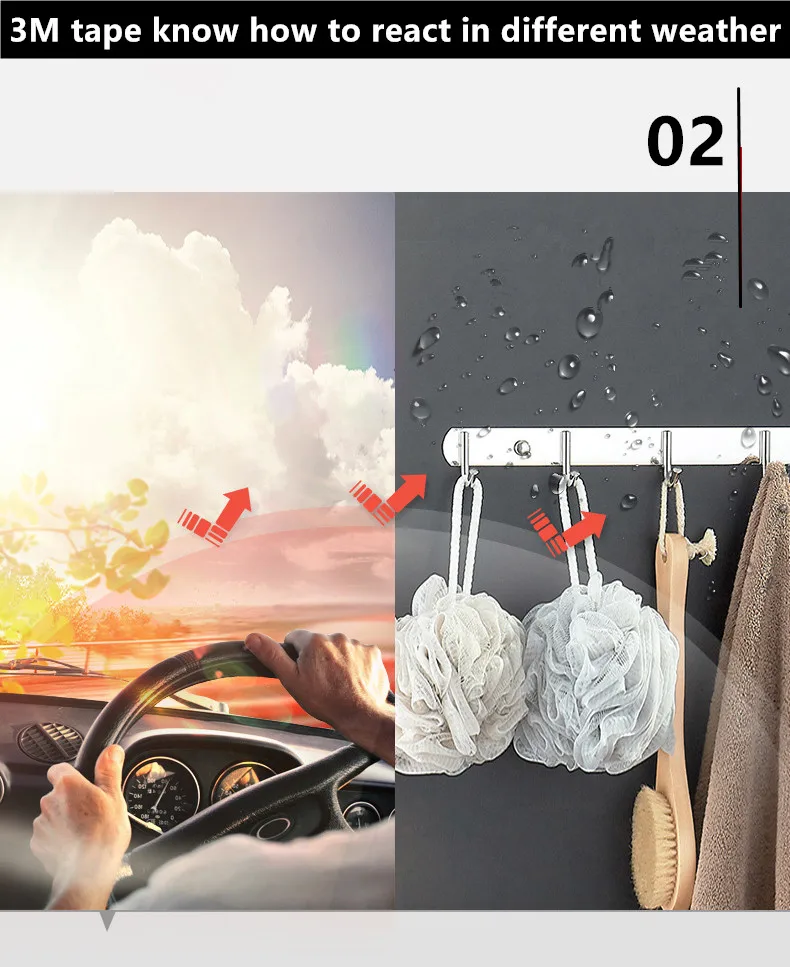

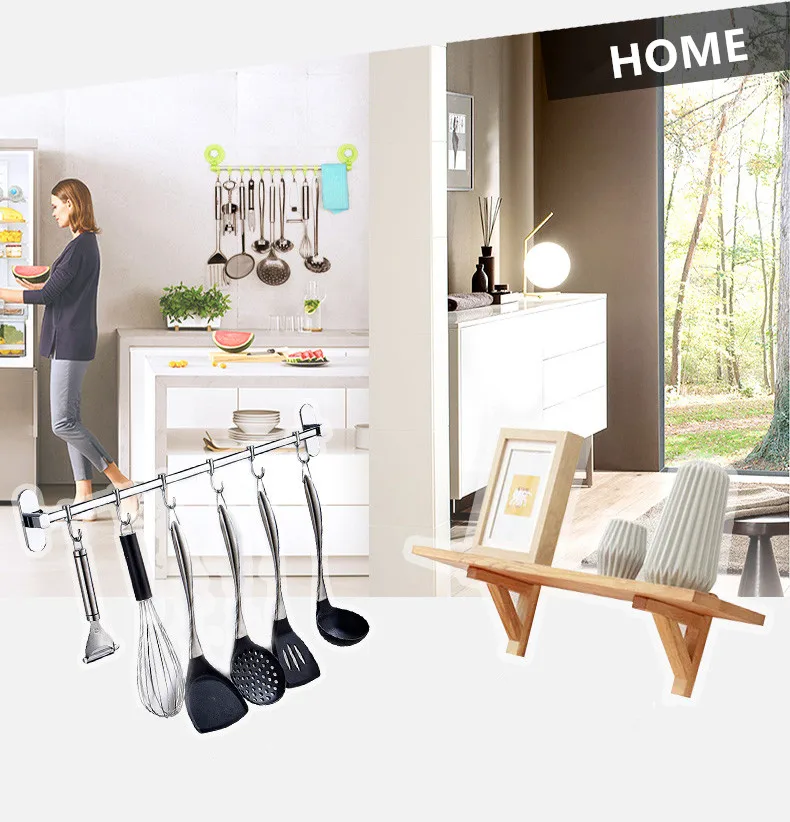
How to use this tape?
Clean: For maximum bond strength,the surface must be clean, dry, smooth, have no rust and oil pollution.Typical cleaning solvents are heptane or isopropyl alcohol.Pressure: Pressure on the adhesive and the surface can help improve bond strength, roller or platen can be used.Time: After application, the bond strength will increase as the adhesive flows onto the surface. At room temperature approximately 50% of ultimate bond strength will be achieved after 20 minutes, 90% after 24 hoursand 100% after 72 hours.Temperature:Ideal application temperature range is 70°F to 100°F (21degree centigrade to 38degree centigrade).Operating temperature should not be below 10 degree centigrade, the temperature is too low, will lead to cure time longer. If temperature is too low, move material and adhesive tape into the warm indoor storage or heating treatment.
What percent of the final bond strength can I expect immediately after application? After 24 hours? After 72 hours?
A. Immediately after an application is made, about 60% of the bond strength is achieved. As the adhesive continues to wet-out the surface, you can expect the bond to be at about 75% - 80% after 24 hours. After 72 hours, 95%+ of the bond strength is achieved. The bond will continue to build with time.
Is the tape solvent resistant?
A. Yes, 3M acrylic foam tapes are resistant to most common automotive solvents like gasoline, diesel fuel, washer solvent, etc. Solvent resistance is a function of type of solvent, time of exposure and temperature.
Why doesn`t the tape feel sticky?
A. 3M`s high performance acrylic adhesives tend to be firm and dry to the touch. They are designed to bond materials other than skin. The adhesives used are designed to give optimum performance and adhesion to automotive substrates and components. The natural oils and moisture of skin can vary from person to person and affect the "thumb appeal" of the 3M Acrylic Foam Tape. To one person the tape can feel very sticky and to another it can feel much less sticky to the touch. The difference in "thumb appeal" is in the variation of the 2 individual`s skin surfaces not the adhesive.
The part is not adhering to the vehicle. What might be wrong?
A. Areas to investigate for poor adhesion or performance include:Check for surface contamination. The substrates must be clean and free of any contaminant. This is the most common cause of poor adhesion.Check for surface match. Are the two surfaces to be bonded a good match?Check for proper application pressure and wet-out.Check the back of the component for flatness.Check the installation process for proper procedures.

Comments
Post a Comment